TRIMEDX Introduces GeoSense, A Real-time location system (RTLS) for health care
TRIMEDX Introduces GeoSense, A Real-time location system (RTLS) for health care
How are you managing and optimizing your clinical assets?
Answering that question is becoming more difficult as you contend with
FAST AND FREQUENT CHANGES:
TRIMEDX being recognized as top 100 at North American Inspiring Workplaces Awards
TRIMEDX being recognized as top 100 at North American Inspiring Workplaces Awards
How are you managing and optimizing your clinical assets?
Answering that question is becoming more difficult as you contend with
FAST AND FREQUENT CHANGES:
TRIMEDX named 2024 top company in medical equipment maintenance services by MedTech Outlook
TRIMEDX named 2024 top company in medical equipment maintenance services by MedTech Outlook
How are you managing and optimizing your clinical assets?
Answering that question is becoming more difficult as you contend with
FAST AND FREQUENT CHANGES:
Black Book™ Research study rates TRIMEDX top clinical engineering provider
Black Book™ Research study rates TRIMEDX top clinical engineering provider
How are you managing and optimizing your clinical assets?
Answering that question is becoming more difficult as you contend with
FAST AND FREQUENT CHANGES:
Unlock The Full Potential of Your Clinical Assets
Unlock The Full Potential of Your Clinical Assets
How are you managing and optimizing your clinical assets?
Answering that question is becoming more difficult as you contend with
FAST AND FREQUENT CHANGES:
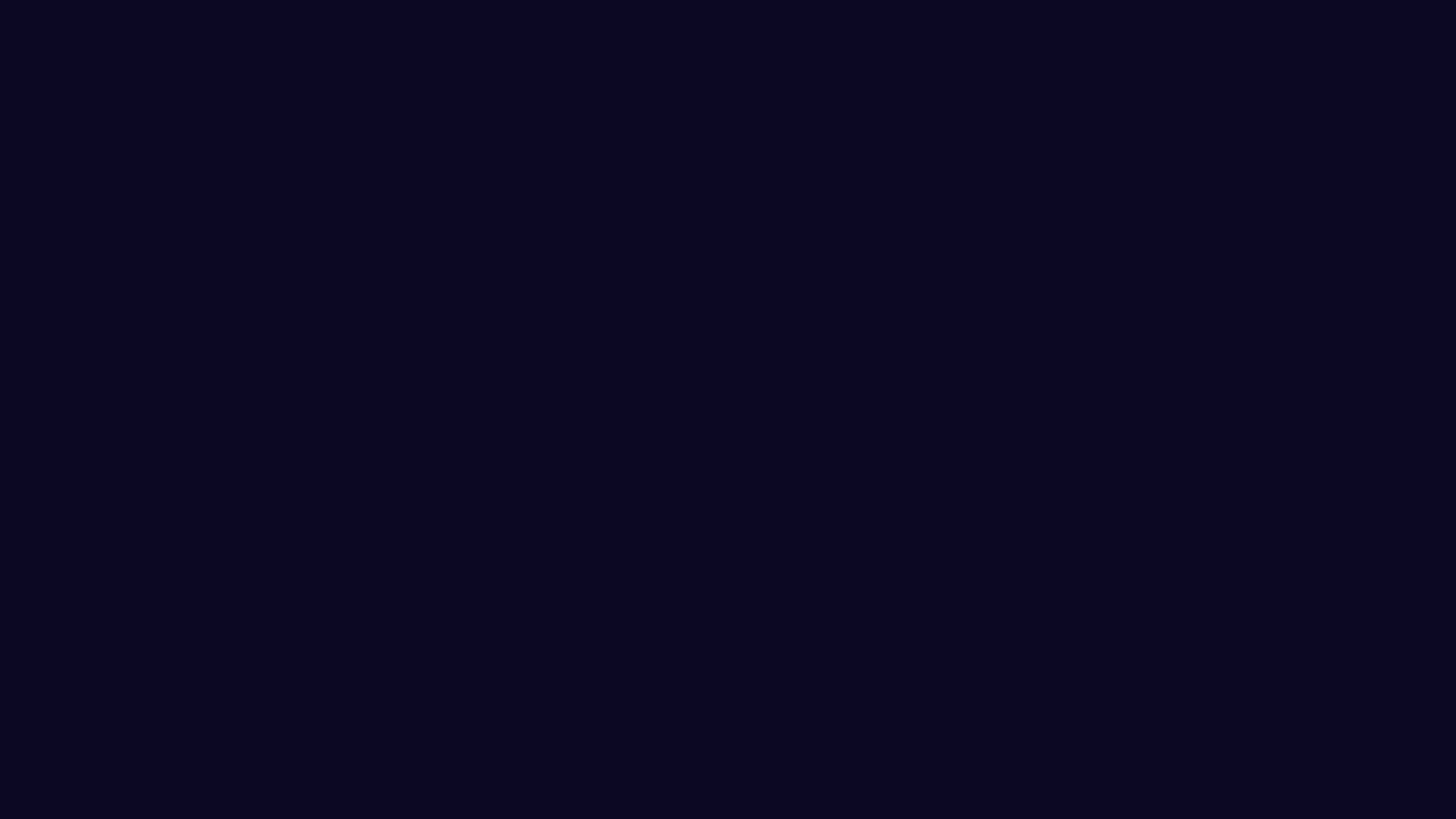
TECHNOLOGY-ENABLED CLINICAL ASSET MANAGEMENT
BUILT BY PROVIDERS FOR PROVIDERS
Budget constraints, workforce burnout, and rising cyberattacks are putting more pressure than ever on health systems. Costly point solutions for managing, servicing, and securing asset inventories are struggling to keep up. That is why TRIMEDX offers comprehensive solutions to maintain, protect, and optimize your clinical assets.
White Paper
4 STRATEGIES FOR ANTICIPATING MEDICAL DEVICE NEEDS TO PROTECT YOUR HEALTH SYSTEM AND PATIENTS
Keeping up with modern healthcare technology is often at odds with the need to manage budgets, leading systems to view their inventories as costly break/fix functions. Download our white paper, originally published with Becker’s Healthcare, to learn new strategies to anticipate medical device needs, improve patient safety, and maximize uptime.
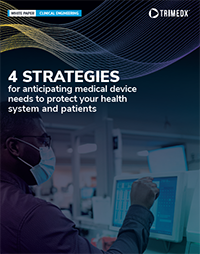
FOOTNOTES
2 TRIMEDX internal data based on findings from 500+ Current State Assessments.
3 McKinsey & Company, The Financial Impact of COVID-19 on Health Systems and How CFOs are Responding, June 2020.